Emotional Intelligence Articles
Learn more about emotional intelligence and leadership by exploring our library of over 300 articles, written by TalentSmartEQ’s thought leaders.
Featured EQ Article
Retention Without Raises: How to Keep Top Talent When Budgets Are Tight
When promotions are paused, hiring is frozen, and compensation budgets are flat, organizations often brace for talent exits. The fear is understandable, and in many cases, justified. But here’s what’s often missed: Most people don’t leave because of the paycheck. According to iHire’s 2024 Talent Retention Report, just 20% of employees cited pay as the primary […]
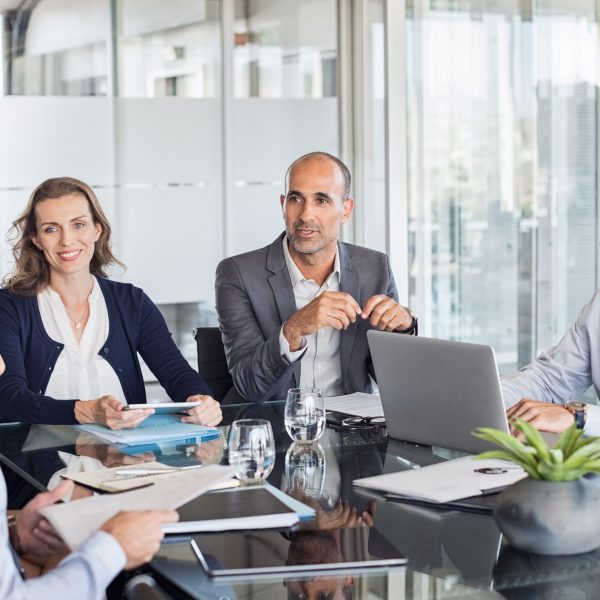
Results
No posts found
Subscribe Today
Subscribe to our EQ Insights newsletter for the latest research, trends and insights on the impact of emotional intelligence.
By completing this form, you consent to receive marketing communications. See our Privacy Policy.